新沂抛丸清理机厂家
发布时间:2022-09-01 01:54:54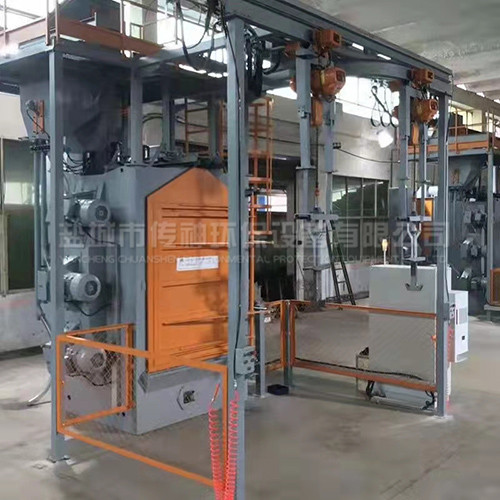
新沂抛丸清理机厂家
吊钩式抛丸机平时维护保养关键点:1、工作中前查验职工中间的工作交接纪录。2、查验是不是有脏物掉入机身,立即消除防止阻塞各运输阶段导致机械故障。3、操作前,应再次检查护板、叶片、离心叶轮、硫化橡胶帘、定项套、辊子等部件的损坏情况,并立即更换。4、查验各家用电器健身运动构件的相互配合,螺钉连接是不是松脱,立即扭紧。5、抛丸清理机机器设备滴油点定期维护各位置充注油是不是符合要求。6、对抛丸清理机的室体护板每日开展查验,有毁坏应先拆换。7、作业员对清除实际效果应随时随地查验,若有异常应先关机,并对机器设备开展总体查验。8、启动前,实际操作人员必须检查控制箱(控制面板)的各种电源开关是否可以在需要设置的位置(包括各电源主开关)启动,以防止误操作,损坏电气设备和工业设备,损坏机械设备。9、液压密封件务必每日查验,如被毁坏马上拆换。10、经常检查不锈钢板的去除质量,必要时可调整弹丸抛射视角和辊道运输速率,并按安全操作规程适当操作。

新沂抛丸清理机厂家
抛丸机是否应采取一些防爆措施,取决于其使用环境、工件类型、使用要求等。如果工件在抛丸过程中会产生爆炸性粉尘,或在某些环境条件下有爆炸风险,则需要采取一定的保护措施,以避免或防止爆炸。抛丸机采取防爆措施的话,在具体措施上,是为:抛丸机除尘器本体内表面无漆膜,本体有散口。在除尘袋上,应选择含金属丝的导电滤袋。此外,在除尘风管上,其法兰接地,并在风管入口侧安装单向逆止阀。抛丸机体接地,风机电机采用防爆型,各部位安装断路器漏电保护器。影响抛丸清理机价格高低的主要因素:1、抛丸速度;抛丸速度增加时,抛丸强度也增加,但速度过高时,抛丸破损量增加。2、抛丸的硬度;当抛丸硬度高于零件硬度时,其硬度值的变化不会影响抛丸强度;当抛丸比零件软时,如果抛丸硬度值降低,抛丸强度也会降低。3、喷射角度;抛丸射流垂直于待喷表面时,抛丸强度高,一般应保持在这种状态。如果零件的形状有限,必须用小角度喷丸,应适当增加喷丸的尺寸和速度。4、抛丸的破碎量;抛丸动能低,破碎的抛丸越多,喷丸强度越低,不规则的碎丸会划伤零件表面。因此,应经常清除碎丸,以确保喷丸完整性大于85%。抛丸设备基本相同,只需使用一些辅助装置来更严格地控制抛丸过程。5、抛丸大小;抛丸越大,冲击动能越大,抛丸强度也越大,但抛丸的覆盖率降低。因此,在保证抛丸强度的同时,应尽量选择较小的抛丸。此外,喷丸尺寸还受零件形状限制。当零件上有沟槽时,抛丸直径应小于沟槽内圆半径的一半。抛丸粒度常在6~50目之间选用。

新沂抛丸清理机厂家
目前被很多行业广泛采用。本机功能技术含量高,可设计pc控制和电气设备自动控制,具有自动监视、自动保护和无级变频调速等装置。可以达到一机多用的目的。其主要原理是抛弃压缩空气的动力作用,采用抛丸器、离心力的抛射,高速抛射工件表面,特别抛射工件内腔死角,达到必要的光亮度、清洁度、粗糙度、加强工件表面的目的,大幅度提高零件的寿命和美观性。抛丸清理机的使用技术:1、抛丸清理机过程中,应尽量在抛丸区内放置工件,提高清扫效率,降低保护板的磨损,延长寿命。2、在工件不能增加的情况下,调整方向套,使投射的钢丸Z大限度地投射到工件上,也可以增加保护板的寿命,减少磨损。3、①除尘系统应调整支管各部门,合理分配风力,提高除尘效果。②吸尘器需要保证定期清灰。

新沂抛丸清理机厂家
抛丸机脱脂的目的是去除工件表面的油污。抛丸后,附着在抛丸上的工件会形成油泥,影响涂层质量。同时,油污会堵塞除尘过滤,导致过滤使用寿命缩短。严重的话会堵塞除尘设备,导致除尘设备报废。卡车厂抛丸线脱脂采用加热喷射处理系统,工艺要求:温度40~70℃;槽液浓度1~5点。生产过程中,应及时调整,以确保达到工艺要求的范围。梁式抛丸线还应控制喷射压力在0.2~0.4兆帕范围内,过低容易清洗,过高容易将工件从挂击落。清洗保养:脱脂槽每周换水一次,彻底清理沉淀物;滤网每2小时清洗一次;喷嘴每天调整一次,方向准确,不堵塞;管道每月清洗两次。洗涤设备类似于脱脂,也采用加热喷射处理系统,但只控制温度(40~70℃),不需要控制浓度,其他管理与脱脂相同。纵梁抛丸线采用压缩空气吹水强制沥水,横梁抛丸线采用旋转离心沥水自动控制。要求工件表面的浮水基本沥干,减轻干燥压力,节约能源。干燥温度应为70~120℃,以保证工件表面的残水清洁。沥水和干燥的管理是去除工件表面的水分。带水工件进入抛丸机的后果比带油工件更严重。首先,带水工件抛丸后容易生锈,影响涂层质量;其次,水进入抛丸机会导致钢丸和抛丸产生的灰尘生锈和结块,导致抛丸机输送系统和除尘系统堵塞,严重时报废。因此,在生产过程中,应确保工件表面的水分被去除。